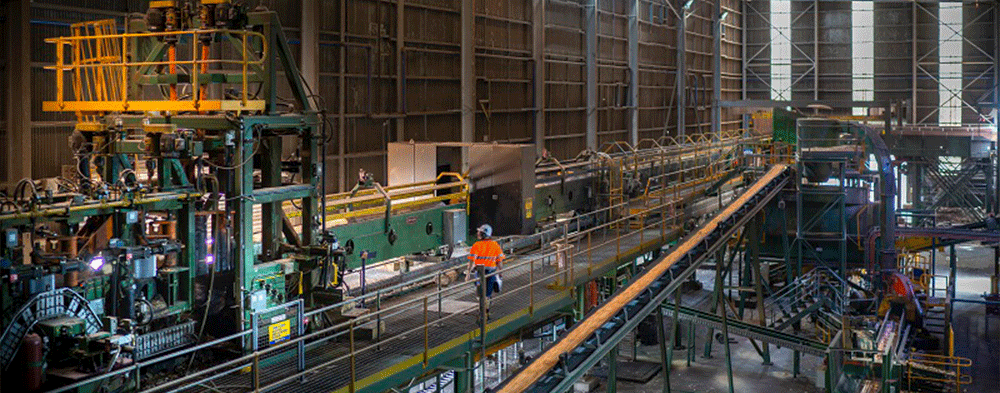
Tasmanian plantation pine is the perfect, sustainable building material. It is locally made, strong, renewable and has the lowest embodied energy of any major building material. And to top it off, timber absorbs carbon dioxide, a key contributor to global warming. For every cubic metre of timber, we make 631 kg of carbon dioxide is taken out of our atmosphere and locked in the timber for its service life.
New-Generation Kiln Uses Fewer Resources to Make Better Timber
At Timberlink, we are always looking for new technologies that can make our environmental footprint even smaller. Which is why we have just spent $4 million to install Tasmania’s first continuous contraflow kiln (CFK) at our Bell Bay mill. This relatively new timber drying technology, uses less electricity and water compared to conventional kilns, yet features a gentler drying process, so it produces timber with lower moisture content variation, providing users with greater stability and increased straightness.
A traditional batch kiln works by loading wet timber into the kiln then heating it at high temperatures multiple times until the right moisture content is reached. Such rapid, intense heating can make the timber brittle and prone to movement. In contrast, our new CFK heats the timber slowly and gently, creating consistently stronger, superior timber products.
So how does the CFK work?
Well, inside the 80-metre long kiln, there are two tracks sitting side by side. Wet timber is loaded onto these tracks at opposite ends of the kiln. These streams of timber are then continuously pushed slowly through the kiln towards each other, taking 16 hours to pass through the full length of the CFK.
The exiting hot, dry wood on one track, exchanges its heat with the new cold, wet wood entering on the other track. By exchanging heat this way, less energy is needed to run the kiln and much of the water that would normally evaporate into the atmosphere, condenses on the wood and so helps to re-condition it.
Data shows the CFK uses 30% less heat energy and 10% less electricity than traditional kilns.
As kiln drying accounts for over 90% of our mill’s total energy use, improving energy efficiency here, significantly reduces our Tasmanian environmental impact even though we generate heat using sustainably grown and harvested sawmill residue.
Why do we use kilns to dry timber?
Drying timber improves its strength, stability, nail holding and gluing properties as well as making it lighter. Drying the timber naturally would take over a year so to speed up the process, we use kilns which can dry timber in as little as 16 hours. Kilns also allow you to control the temperature and humidity, ensuring the timber is dried evenly so it is more stable which is another way of saying less likely to move and no longer be straight
In addition to these benefits, the improvement in efficiency gives our Bell Bay mill the ability to make more timber products if extra plantation logs become available. Australia is a net importer of wood products, including structural softwood timber and Timberlink’s new CFK will enable the replacement of product that currently needs to be imported, mainly from Europe, with domestically manufactured timber. This will reduce Australia’s reliance on imported timber and the environmental cost of shipping timber from one side of the world to the other.
With all these benefits, you can see why we were so keen to invest in this exciting technology and be the first to bring it to Tasmania and we haven’t even started on the social benefits the CFK can bring through upskilling our employees in the latest kiln drying technology but that’s a subject for another blog.